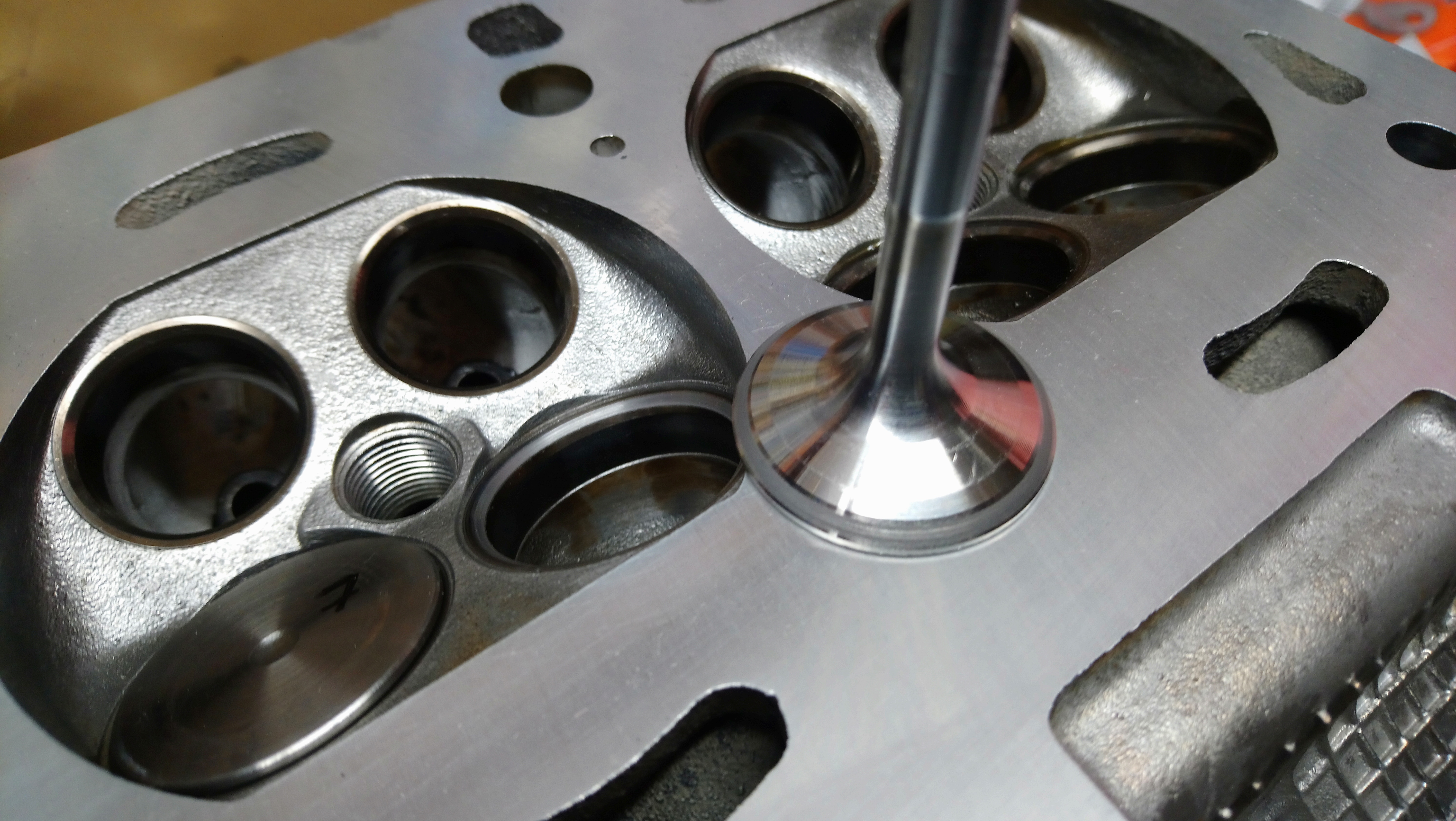
Ventile einschleifen
Da der Zylinderkopf nun sauber und überprüft worden ist, steht das Einschleifen der neuen Ventile auf dem Plan.
Ich habe mich ausdrücklich für einen komplett neuen Ventilsatz entschieden, damit ich die noch geraden Ventile nicht reinigen muss, was auch einen erheblichen Zeitaufwand darstellt. Ich müsste mir sonst außerdem noch Messmittel organisieren, mit denen ich die Rundlaufgenauigkeit der Ventile überprüfen kann. – Bei neuen Ventilen kann ich mir sicher sein, dass diese rund laufen und die Dichtfläche nicht eingeschlagen ist.
Methoden zum Einschleifen der Ventile
Für das Einschleifen der Ventile gibt es mehrere Möglichkeiten:
- Holzstab mit Gummisauger, der auf dem Ventilteller festgesaugt wird
- Benzinschlauch über dem Ventilschaft und das Ventil von der anderen Seite des Zylinderkopfes drehen
- Ein automatisches Ventileinschleifgerät, für den Einsatz mit der Bohrmaschine / Akkuschrauber
Welche Methode letztendlich angewandt wird, um zu einem guten Tragbild an der Dichtfläche zu kommen, spielt keine Rolle.
Ich habe mich für die „klassische“ Methode mit dem Holzstab mit Gummisauger entschieden, da man bei dieser Methode das beste Gefühl dafür hat, wann das Ventil richtig eingeschliffen ist. Man hört es sehr deutlich am Klang während des Einschleifvorgangs und auch beim Abheben des Ventils vom Sitz saugt sich ein fertig eingeschliffenes Ventil leicht fest.
Die Methode mit dem Benzinschlauch am Ventilschaft funktioniert auch, ist aber insofern umständlich, da man den Zylinderkopf auf die Seite legen muss. Auch stelle ich mir die Arbeitshaltung wenig ergonomisch vor.
Das automatische Ventileinschleifgerät, auch „Ventilteufel“ genannt, bietet eine wirkliche Zeitersparnis, aber wenn man (wie meine Wenigkeit) diese Arbeit zum ersten Mal durchführt, kann man relativ schnell die Ventilsitze zu weit aufschleifen und dann ist guter Rat teuer, ja sehr teuer sogar! 🙁 Auch übertönt der Motor der Bohrmaschine oder des Akkuschraubers die Schleifgeräusche und es fehlt daher eine Rückmeldung wie weit fortgeschritten der Schleifvorgang ist. – Ich denke dieses Werkzeug ist eher den Profis vorbehalten, da man wirklich Erfahrung mitbringen muss, um ein gutes Ergebnis zu erzielen.
Letztendlich funktioniert das Einschleifen der Ventile durch eine oszillierende Links- und Rechtsdrehung der Ventile, während auf der Dichtfläche eine Schleifpaste aufgetragen ist. Dabei ist es wiederum wichtig, dass man das Ventil regelmäßig um ca. eine viertel Umdrehung (90°) weiter bewegt und dann erneut ansetzt, damit die Dichtfläche sich gleichmäßig anpasst. Das automatische Ventileinschleifgerät setzt mittels eines Getriebes die Drehbewegung der Bohrmaschine in eine oszillierende Bewegung um, aber auch hier muss man das mit der Hand gehaltene Getriebe von Zeit zu Zeit loslassen, damit sich das Ventil in eine neue Stellung bewegt.
Benötigtes Werkzeug
Ich habe mich für die Holzgriffe mit Gummisaugnapf von Hazet entschieden, da diese einen verjüngten Schaft am oberen Ende aufweisen und dadurch deutlich besser in der Handhabung sind als ihre Pendants mit geraden Holzstielen. Es gibt sie in verschiedenen Größen, damit der Saugnapf für die Ventile passend ausgewählt werden kann. Die drei kleinsten Größen tun es für diese Ventile ganz hervorragend und wer weiß wann ich das nächste Mal wieder Ventile einschleifen muss?
- Hazet 795-1, Durchmesser Saugnapf: 20 mm
- Hazet 795-2, Durchmesser Saugnapf: 25 mm
- Hazet 795-3, Durchmesser Saugnapf: 30 mm
Angefangen wird mit der Reinigung des Ventils und der Ventilsitzrings von etwaigen Rückständen und Ölen. Es ist insbesondere darauf zu achten, dass keine Verunreinigungen oder gar Ventilschleifpaste bei dieser Arbeit in die Ventilführungen gelangt, da dann der Ventilschaft und die Ventilführung durch die Drehbewegung des Ventils beschädigt werden. Am besten reinigt man nach getaner Arbeit den Zylinderkopf noch einmal vollständig.
Die Ventileinschleifpaste Teroson VR2200 von Henkel besteht aus 2 Pasten in einer Doppeldose: Eine grobe Vorschleifpaste mit einer Korngröße über 90 µm, welche man nur bei sehr stark verschmutzten Ventilsitzen benötigt und eine Nachschleifpaste mit Korngrößen unter 90 µm, welche ein feines Schleifbild für eine gute Abdichtung hat. Es gibt auch andere Hersteller von Schleifpasten und für welche ihr Euch letztendlich entscheidet, spielt keine Rolle.
Das Einschleifen
Man trägt die Schleifpaste gleichmäßig auf die Dichtfläche des Ventils auf und setzt dieses in die entsprechende Ventilführung am Zylinderkopf ein. Den Ventilschaft gilt es einzuölen, damit das Ventil beim Einschleifen nicht beschädigt wird und diese Arbeit auch etwas einfacher von statten geht.
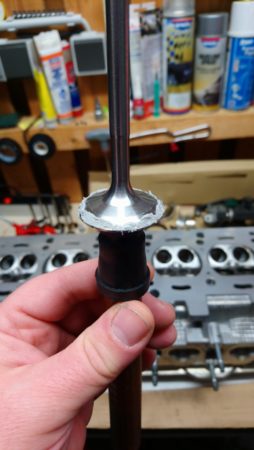
Jetzt setzen wir das Ventil in die Ventilführung ein und fangen an den Holzgriff zwischen den Handflächen hin und her zu drehen. Wer schon einmal versucht hat mittels Feuerbohren ein Feuer zu entzünden, weiß ganz automatisch was er jetzt tun muss! 🙂
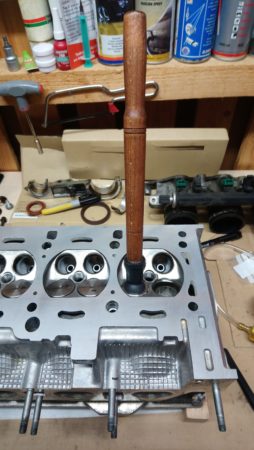
Beim Einschleifen selbst hört man an dem knirschelnden Geräusch wie die Schleifpaste sich zwischen den Dichtflächen befindet und dort abrasiv tätig ist. Dieses Geräusch lässt nach einigen Sekunden schleifen nach und der Ton wird heller und leiser. Nun hebt man das Ventil ab und dreht es eine viertel Umdrehung weiter und fängt erneut an.
Beim Einschleifen drückt sich die Ventilschleifpaste auch von der Dichtfläche weg, sodass man gelegentlich das Ventil entfernen und die Schleifpaste erneut auf die Dichtfläche auftragen sollte. Dazu muss man keine frische Schleifpaste nehmen, sondern es reicht vollkommen aus den zum Ventilschaft hin gedrückten Teil wieder mit dem Finger auf die Dichtfläche zu schmieren.
Überprüfung des Tragbildes
Nach einigen Minuten kann man das Schleifbild überprüfen: Dazu wird die Schleifpaste vom Ventil und Ventilsitz entfernt und das Werk optisch begutachtet: Es muss sich eine gleichmäßige graue Fläche an Ventilsitz und Ventildichtfläche befinden.
Ist die Dichtfläche noch nicht gleichmäßig genug, trägt man erneut Ventilschleifpaste auf und macht das ganze noch einmal. Ein korrekt eingeschliffenes Ventil sieht wie in der nachfolgenden Abbildung aus. Es ist sehr deutlich die matt-graue Dichtfläche an Ventil und Ventilsitz zu erkennen.
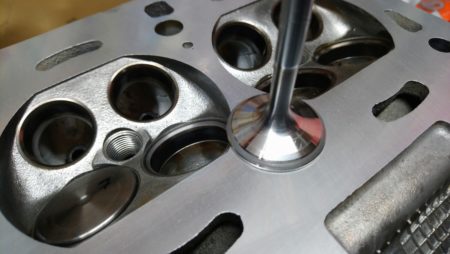
Nummerierung der Ventile / Lagerböcke
Da alle Ventile aus dem Zylinderkopf für die Endreinigung noch einmal entfernt werden müssen und es dann später keine Verwechslung gibt, sollte man die Ventile durchnummerieren. Dies geschieht am einfachsten mittels eines Permanentmarkers auf dem Boden des Ventiltellers.
In aller Regel fängt man bei Zylinder 1 an, welcher direkt am Riemen- oder Kettentrieb liegt und nummeriert alle Einlassventile der Reihe nach durch, ebenso wie sie Auslassventile. Da die Ventildurchmesser zwischen Ein- und Auslassventilen in aller Regel unterschiedlich sind, kann man Ein- und Auslassventile nicht vertauschen. Bei ientischem Ventildurchmesser empfiehlt es sich zusätzlich ein A für Auslass- oder ein E für Einlassventil auf den Ventilboden zu schreiben.
Bei mir gab es also 10 Einlassventile und 10 Auslassventile, jeweils nummeriert von 1 bis 10, wobei jeweils 2 für einen Zylinder zuständig sind:
- Zylinder 1: Ventile 1 & 2
- Zylinder 2: Ventile 3 & 4
- Zylinder 3: Ventile 5 & 6
- Zylinder 4: Ventile 7 & 8
- Zylinder 5: Ventile 9 & 10
Genauso verfährt man mit den Nockenwellen- bzw. Kurbelwellenlagerböcken: Bei meinem Motor waren diese nicht nummeriert, was bei identischen Teilen beim späteren Zusammenbau schwierig wird. Die Nockenwellen- und auch die Kurbelwellenlagergasse wird zusammen mit den Lagerböcken gebohrt und daher sind diese Teile nicht identisch, obwohl sie gleich aussehen! Hier kommt es auf jeden 1/100 Millimeter an.
Für das spätere Funktionieren des Motors ist es enorm wichtig, jeden Lagerbock wieder an seine ursprüngliche Stelle zu montieren!
Dichtigkeitstest
Hat man nun alle Ein- oder Auslassventile eines Zylinders eingeschliffen, kann man diese mittels eines Unterdrucktests auf Dichtigkeit überprüfen. Fällt dieser Test negativ aus, so muss man sich die Dichtfläche noch einmal sehr genau anschauen und an dem undichten Ventil noch einmal nachgearbeitet werden.
Bei dichten Ventilen ist es trotz fehlender Ventilschaftabdichtungen ohne weiteres möglich mit einer einfachen Handpumpe mehr als -0,5 Bar Unterdruck zu erzeugen, welcher dann auch recht langsam abfällt.
Mit Unterdruck überprüfte Ventile sind auch im späteren Motorbetrieb 100% dicht und dies ist einer genauere Aussage, als das Einfüllen von leicht flüchtigen Flüssigkeiten in den Brennraum oder die Kanäle des Zylinders.
Bei diesem Test liegen die Ventile dabei nur durch ihr Eigengewicht auf den Ventilsitzen und werden nicht durch Ventilfedern in den Sitz gezogen. So kann man schnell ein Ventil entnehmen, nacharbeiten und erneut testen.

Im Prinzip ist diese Arbeit nicht wirklich schwer, aber man muss eine gewisse Sorgfalt und vor allen Dingen Geduld an den Tag legen! Je sorgfältiger und genauer man bei dieser Arbeit vorgeht, desto besser werden die Kompressionswerte des fertig zusammengebauten Motors sein.
Ohne Fleiß kein Preis. (Hesiod, griech. Dichter)
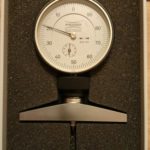
Die Tiefe der einzelnen Ventile in den Brennräumen überprüft man am besten mit einem Tiefenmaß. Somit lässt sich feststellen, ob die Ventile gleichmäßig tief in den Ventilsitzen liegen. Ich benutze für diese Arbeit eine Tiefenmessuhr.
Jetzt gilt es diese Arbeit für die restlichen 18 noch verbleibenden Ventile durchzuführen! 🙂 Ein 5-Zylinder-Motor mit 20 Ventilen hat eine wunderschöne Laufkultur, aber in solchen Momenten fragt man sich, warum man keinen 8-Ventiler fährt…
3 Gedanken zu „Ventile einschleifen“
Hallo, vielen Dank für die Anleitung. Es ist sehr gut Beschrieben.
Jedoch habe ich eine Frage. Können Sie den Druckabfall von dem Unterdruck näher Beschreiben? Bei mir geht der Druck auf -0,6 Bar, aber fällt dann auch innerhalb von 4 bis 5 Sekunden auf 0 Bar herunter. Ist das bei Ihnen auch so? Wie lange bleibt bei Ihnen der Druck bestehen.
Viele Grüße
Martin
Hallo Martin,
-0,6 bar ist ein guter Wert! Wenn Ventilsitz und Ventil mit Bremsenreiniger entfettet sind und der Ventilschaft eingeölt ist, dann ist es völlig in Ordnung, wenn der Unterdruck innerhalb von 4-5 Sekunden wieder abfällt. Wichtig ist, dass sich überhaupt ein Unterdruck mit der Handpumpe aufbauen lässt, denn dann ist das Ventil ausreichend dicht. Schließlich wird es auch von keiner Ventilfeder in den Dichtsitz gezogen, oder?
Es ist jetzt nicht so, dass man da Minuten lang Unterdruck stehen lassen kann. Der Druck fällt immer wieder ab, bei einigen Ventilen schneller, bei anderen langsamer. Wichtig ist wie gesagt, dass Du mit den unterbrochenen Pumpenhüben einer Handpumpe erst einmal einen solchen Unterdruck überhaupt aufbauen kannst und das Tragbild nach dem Einschleifen am Sitz und Ventil gleichmäßig ist. Im späteren Motorbetrieb haben wir es mit wesentlich höheren Drücken und dadurch auch besserer Abdichtung zu tun.
Viele Grüße!
Sven
Vielen Dank für die schnelle Antwort. Ja es sind noch keine Ventilfedern verbaut.
Danke für Ihre Hilfe.